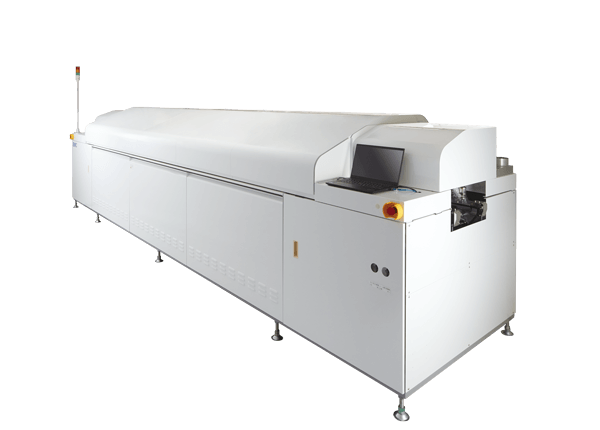
Further improvement in productivity and high functionality
A next-generation environmentally-conscious reflow oven
Further improvement in productivity
- New flux collection unit and cooling mechanism that enables reduction in downtime
- Extends maintenance cycle and enables maintenance in a short time period
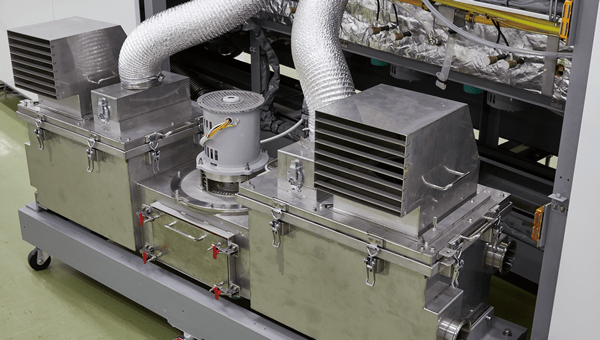
New flux collection unit
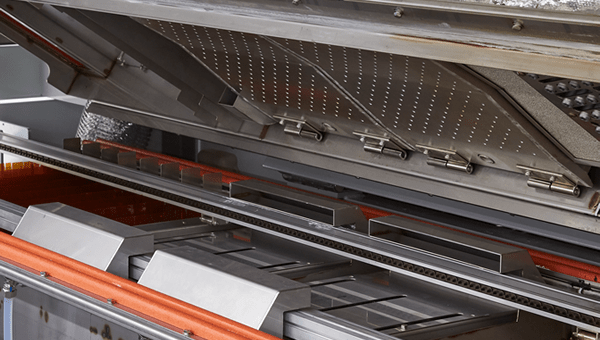
New cooling mechanism
Environmental-conscious
- The internal structure of the oven is redesigned to contribute to carbon neutrality, further reducing the amount of electricity and nitrogen used
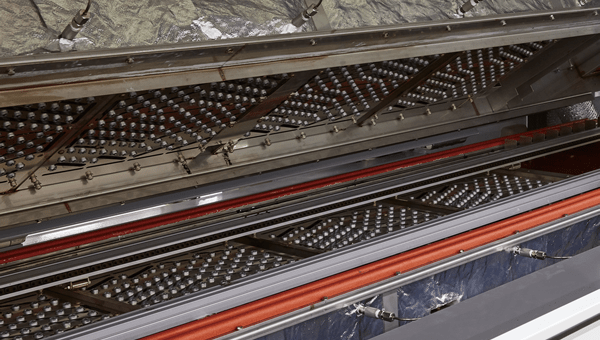
New heating unit with further improved
thermal efficiency
Achieves about 10% reduction
in power consumption
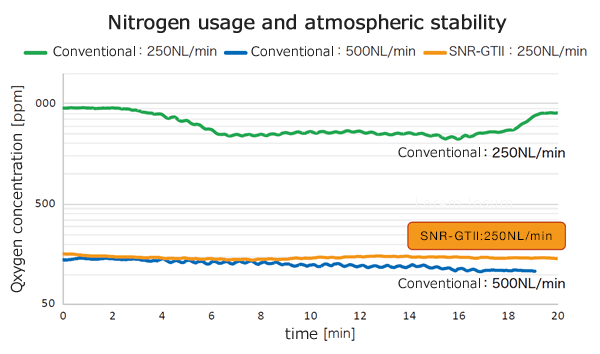
Nitrogen consumption is halved by thorough
verification of the circulation route in the oven
Easy to use high functionality
The operation screen is redesigned in consideration of reducing the operational load at the production site. The operation screen realizes an intuitive operation feeling and is designed so that anyone can learn to use it in a short time.
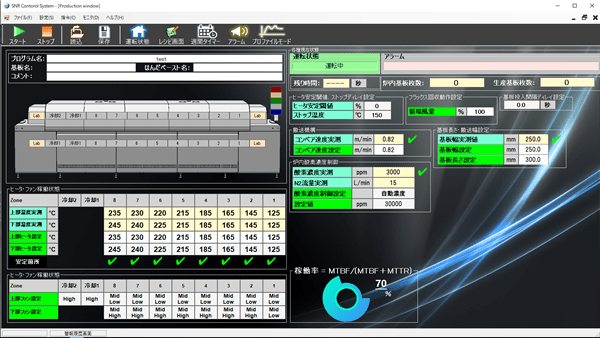
Multiplexing and remote operation of the operating system is realized by adding operating devices (some are optional).
Such configuration reduces t he risk o f m achine t rouble and enables the user to handle troubleshooting remotely.
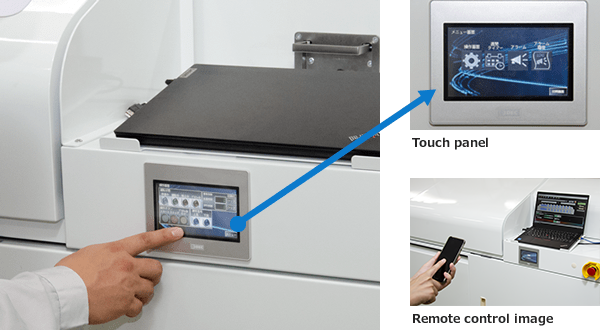
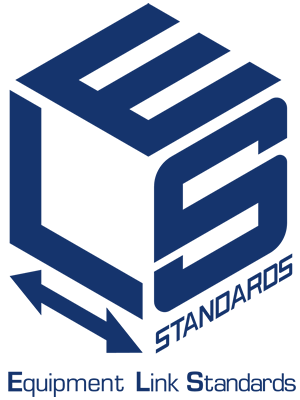
Can be linked with various companies' installed equipment and production management systems, including ELS communication specifications [JARAS1014], which a re communication specifications for next-generation smart factories.
Operation by Laptop PC
The operation screen is redesigned in consideration of reducing the operational load at the production site.
The operation screen realizes an intuitive operation feeling and is designed so that anyone can learn to use it in a short time.
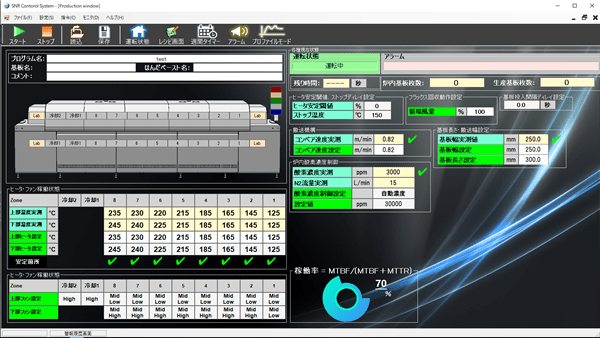
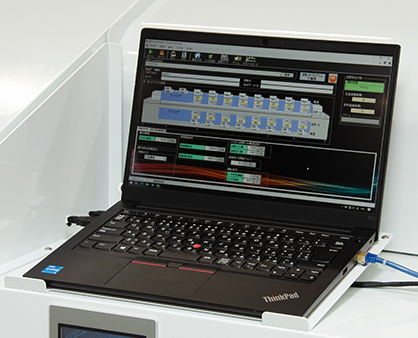
New heating unit with further improved thermal efficiency
Achieves about 10% reduction in power consumption
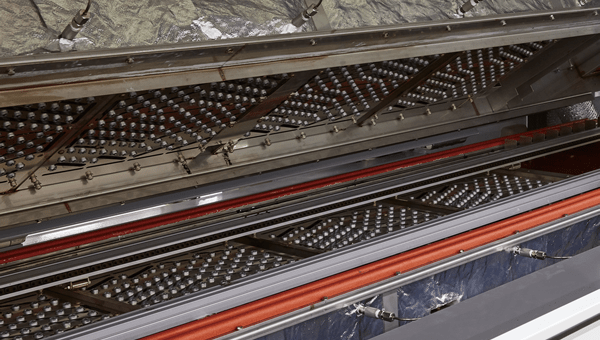
Other equipment
- PLC + PC control
- Heated zone flux management system
- PCB fall/congestion sensor
- PCB counter
- Oxygen analyzer
- Automatic oxygen concentration control
- 3-block fan control
- Temperature profile measurement mode
- Weekly timer
- Signal tower
Flux collection unit enhancement
By adding a water-cooling coil fin, radiator, and chiller unit (external) in addition to the standard air-cooled pipe, the recovery capacity according to the amount of solder paste used is realized.
Solder paste usage / month | 60kg or less | 60〜80kg | 80kg or more | |
---|---|---|---|---|
Selection | A(STD) | B(OP) | C(OP) | |
Unit | Air cooling pipe | ○ | ○ | ○ |
Water cooling coil fin | - | ○ | ○ | |
Radiators | - | - | ○ | |
Chiller unit | - | ○ | ○ |

New flux collection unit
Other optional equipment
- KIC system collaboration
- Operator mode/Engineer mode
- B(Breeze) Specification optional
- Automatic changeover by bar code
- PCB warp prevention mechanism
- Oven center exhaust duct
- In-out feeder free rollers
- UPS
- All block fan control
- Safety light curtain
- Mesh conveyor
- SMEMA signal line
- Automatic width adjustment(conveyor rail)
- Automatic width adjustment(warpage prevention rail)
- Display in English/Chinese
SNR-825GT Ⅱ | SNR-840GT Ⅱ | |||
---|---|---|---|---|
Dimensions (L×W×H) | 5,300 x 1,300 x 1,420 mm | 5,700 x 1,550 x 1,420 mm | ||
Conveyor height | 900±20 mm | 900±20 mm | ||
Conveyor speed | 0.3 - 2.0 m/min | 0.3 - 2.0 m/min | ||
Board dimensions | W: 50 - 250, L: 100 - 400, T: 0.8 - 3.0 mm | W: 50 - 400, L: 100 - 400, T: 0.8 - 3.0 mm | ||
Component height | ≦30mm [OP: 35mm], ≧25mm | ≦30mm [OP: 35mm], ≧25mm | ||
Heated zones | 8 | 8 | ||
Cooling zones | 2 | 2 | ||
Side edge clearance(select one) | 3 or 4 or 5 mm | 3 or 4 or 5 mm | ||
N2(Nitrogen) gas supply | ≧99.999%, ≧0.4MPaG, max. 400NL/min | ≧99.999%, ≧0.4MPaG, max. 600NL/min | ||
N2 (Nitrogen) gas usage | Component height/STD:≦30mm、≧25mm | 250NL/min | 400NL/min | |
Component height/OPT:≦10mm、≧10mm | 150NL/min | 250NL/min | ||
Power requirement | 200V, max. 38kW, 110A, 3-phase | 200V, max. 47kW, 135A, 3-phase | ||
SNR-850GT Ⅱ | SNR-1025GT Ⅱ | |||
Dimensions (L×W×H) | 5,700 x 1,550 x 1,420 mm | 6,000 x 1,300 x 1,420 mm | ||
Conveyor height | 900±20 mm | 900±20 mm | ||
Conveyor speed | 0.3 - 2.0 m/min | 0.3 - 2.0 m/min | ||
Board dimensions | W: 50 - 500, L: 100 - 500, T: 0.8 - 3.0 mm | W: 50 - 250, L: 100 - 400, T: 0.8 - 3.0 mm | ||
Component height | ≦30mm [OP: 35mm], ≧25mm | ≦30mm [OP: 35mm], ≧25mm | ||
Heated zones | 8 | 10 | ||
Cooling zones | 2 | 2 | ||
Side edge clearance(select one) | 3 or 4 or 5 mm | 3 or 4 or 5 mm | ||
N2(Nitrogen) gas supply | ≧99.999%, ≧0.4MPaG, max. 600NL/min | ≧99.999%, ≧0.4MPaG, max. 400NL/min | ||
N2 (Nitrogen) gas usage | Component height/STD:≦30mm、≧25mm | 400NL/min | 280NL/min | |
Component height/OPT:≦10mm、≧10mm | 250NL/min | 180NL/min | ||
Power requirement | 200V, max. 47kW, 135A, 3-phase | 200V, max. 47kW, 135A, 3-phase | ||
SNR-1040GT Ⅱ | SNR-1050GT Ⅱ | |||
Dimensions (L×W×H) | 6,400 x 1,550 x 1,420 mm | 6,400 x 1,550 x 1,420 mm | ||
Conveyor height | 900±20 mm | 900±20 mm | ||
Conveyor speed | 0.3 - 2.0 m/min | 0.3 - 2.0 m/min | ||
Board dimensions | W: 50 - 400, L: 100 - 400, T: 0.8 - 3.0 mm | W: 50 - 500, L: 100 - 500, T: 0.8 - 3.0 mm | ||
Component height | ≦30mm [OP: 35mm], ≧25mm | ≦30mm [OP: 35mm], ≧25mm | ||
Heated zones | 10 | 10 | ||
Cooling zones | 2 | 2 | ||
Side edge clearance(select one) | 3 or 4 or 5 mm | 3 or 4 or 5 mm | ||
N2(Nitrogen) gas supply | ≧99.999%, ≧0.4MPaG, max. 600NL/min | ≧99.999%, ≧0.4MPaG, max. 600NL/min | ||
N2 (Nitrogen) gas usage | Component height/STD:≦30mm、≧25mm | 430NL/min | 430NL/min | |
Component height/OPT:≦10mm、≧10mm | 280NL/min | 280NL/min | ||
Power requirement | 200V, max. 62kW, 200A, 3-phase | 200V, max. 62kW, 200A, 3-phase | ||
SNR-1225GT Ⅱ | SNR-1240GT Ⅱ | |||
Dimensions (L×W×H) | 6,730 x 1,300 x 1,420 mm | 7,130 x 1,550 x 1,420 mm | ||
Conveyor height | 900±20 mm | 900±20 mm | ||
Conveyor speed | 0.3 - 2.0 m/min | 0.3 - 2.0 m/min | ||
Board dimensions | W: 50 - 250, L: 100 - 400, T: 0.8 - 3.0 mm | W: 50 - 400, L: 100 - 400, T: 0.8 - 3.0 mm | ||
Component height | ≦30mm [OP: 35mm], ≧25mm | ≦30mm [OP: 35mm], ≧25mm | ||
Heated zones | 12 | 12 | ||
Cooling zones | 2 | 2 | ||
Side edge clearance(select one) | 3 or 4 or 5 mm | 3 or 4 or 5 mm | ||
N2(Nitrogen) gas supply | ≧99.999%, ≧0.4MPaG, max. 400NL/min | ≧99.999%, ≧0.4MPaG, max. 600NL/min | ||
N2 (Nitrogen) gas usage | Component height/STD:≦30mm、≧25mm | 300NL/min | 450NL/min | |
Component height/OPT:≦10mm、≧10mm | 200NL/min | 300NL/min | ||
Power requirement | 200V, max. 60kW, 250A、3-phase | 200V, max. 75kW, 250A, 3-phase | ||
SNR-1250GT Ⅱ | ||||
Dimensions (L×W×H) | 7,130 x 1,550 x 1,420 mm | |||
Conveyor height | 900±20 mm | |||
Conveyor speed | 0.3 - 2.0 m/min | |||
Board dimensions | W: 50 - 500, L: 100 - 500, T: 0.8 - 3.0 mm | |||
Component height | ≦30mm [OP: 35mm], ≧25mm | |||
Heated zones | 12 | |||
Cooling zones | 2 | |||
Side edge clearance(select one) | 3 or 4 or 5 mm | |||
N2 (Nitrogen) gas supply | ≧99.999%, ≧0.4MPaG, max. 600NL/min | |||
N2 (Nitrogen) gas usage | Component height/STD:≦30mm、≧25mm | 450NL/min | ||
Component height/OPT:≦10mm、≧10mm | 300NL/min | |||
Power requirement | 200V, max. 75kW, 250A, 3-phase |